Tips for Minimizing Downtime in Fluid Control Systems
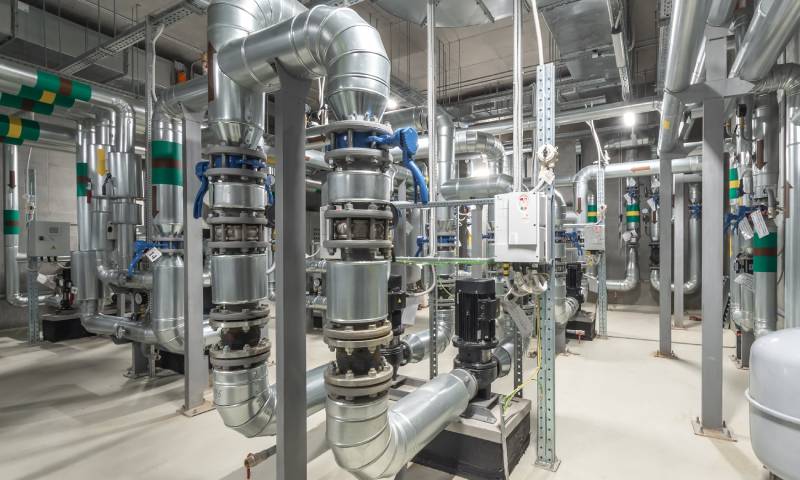
Continuous operations of fluid control systems are critical for industries reliant on efficient processes. Unexpected downtime will lead to lost productivity, increased costs, and frustrated stakeholders. Minimize downtime for your fluid control system with expert tips to keep your system running at peak efficiency.
1. Use High-Quality Components
The foundation of any reliable fluid control system is the quality of its components. When selecting valves, seals, pumps, or piping, it’s essential to invest in well-made, durable parts that can withstand operational pressure and environmental conditions. Poor-quality components often fail prematurely, leading to unnecessary downtime. Reputable suppliers provide certifications and testing data, which can guide you in making the right purchasing decisions.
2. Leverage Real-Time Monitoring Systems
Modern technology offers tools that enable real-time monitoring of fluid control systems. Sensors and IoT (Internet of Things) devices can track pressure levels, flow rates, and potential leaks. These devices can also deliver alerts when performance begins to deviate from expected parameters. For instance, integrating smart flowmeters and monitoring software allows for proactive maintenance, allowing you to address minor issues before they lead to major failures.
3. Train Technicians and Staff
Employing a highly skilled team can make a huge difference when maintaining your fluid control systems. Regularly train technicians and staff on system operations, troubleshooting, and proper maintenance protocols. When employees are confident in diagnosing issues, they can respond faster to potential problems, significantly reducing downtime. Consider conducting on-site workshops or leveraging online training programs tailored to fluid control systems to keep skills sharp.
4. Stock Critical Spare Parts
Waiting for the delivery of replacement parts during a breakdown can extend downtime unnecessarily. Stocking critical spare parts ensures that you can quickly address issues as they arise. When assessing inventory needs, prioritize components that are prone to wear and tear, such as gaskets, seals, and valves. For example, selecting the right ball valves as spares can be key to ensuring seamless operations, as these parts are often central to controlling fluid flow.
5. Optimize System Design
The design of your fluid control system plays a pivotal role in its reliability. Overly complex systems can introduce unnecessary points of failure, while poorly laid-out systems may make maintenance more difficult. Collaborate with experienced engineers to streamline system layouts and ensure accessibility for routine inspections and repairs.
Minimizing downtime in fluid control systems requires a multifaceted approach. Following the steps above helps you significantly improve the reliability and efficiency of your systems. If you want to keep your operations running at peak performance, take action today to evaluate and enhance your fluid control systems.
Would you like to receive similar articles by email?

